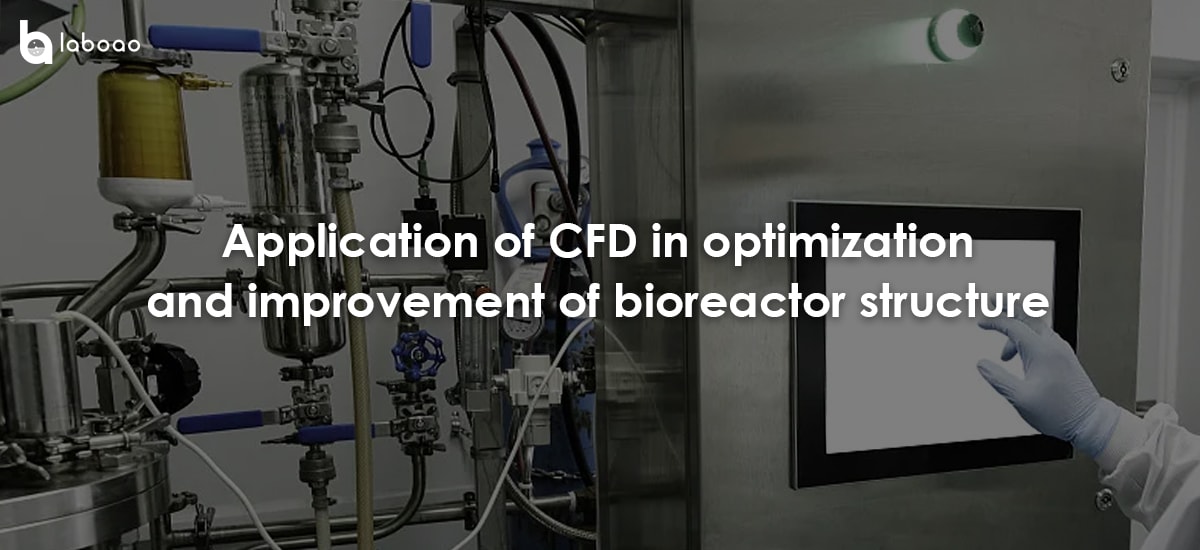
Bioreactor is an irreplaceable main equipment in large-scale culture of animal cells. Animal cell bioreactor simulates the internal environment of organisms. In order to obtain the effect of high-density proliferation of animal cells and to ensure efficient secretion of animal cells, it is necessary to Control the operating parameters of its culture.
3D model of the 200L tetanus reactor for flow field simulation. The model includes all the volume below the liquid level and part of the volume above the liquid level
In this article, computational fluid dynamics (CFD) is used to optimize and improve the reactor structure and size that affect the efficient secretion of animal cells.
The animal cell bioreactor is a system that simulates the internal environment of animals and conducts biological culture in vitro. It is a high-tech product integrating mechanics, fluids, control, biology and other disciplines. The parameters it controls mainly include temperature, dissolved oxygen, pH, fluid dynamics, nutrients, and the concentration of metabolites.
The ultimate goal is to achieve high-density cell growth and efficiently produce target products such as enzymes, monoclonal antibodies, and vaccines with medical value. Compared with the traditional biological products production process, which has many shortcomings such as long production cycle, cumbersome operations, heavy workload, and easy contamination, the bioreactor system has better stability and safety, saving a lot of labor, production space and energy consumption. , reducing production costs and having obvious advantages.
Studies have shown that bioreactor culture process parameters have a strong impact on cell metabolism and viral titers. In view of the impact of different bioreactors and different culture methods on the quality of biological products, this article reviews the current research status of animal cell bioreactors, the structures and principles of different types of animal cell bioreactors, and structural optimization, aiming to provide It provides a certain reference for selecting bioreactors that are more suitable for culture processes in practical applications of biological product development and production.
Structure and principles of different types of animal cell bioreactors
According to different mixing methods, they are divided into stirred and non-stirred bioreactors. The biggest disadvantage of stirred bioreactors is cell damage caused by shear force. Although continuous improvements have been made, this problem is still difficult to avoid. In contrast, non-stirred reactors produce less shear and are advantageous in animal cell culture.
Average shear strain rate during the stirring rotation period on two longitudinal sections (1/s)
stirred bioreactor
The stirring paddle rotates to drive the liquid flow, thereby providing power for liquid phase stirring. Its structure is similar to a traditional microbial fermentation tank, with the main difference being the structure of the agitator. Since animal cells do not have cell walls, they are very sensitive to shear force. In order to avoid cell damage, the stirred reactor has been improved, including improving the propeller, air supply method, adding accessories, etc., to further optimize the conditions for suitable cell growth. environment.
The form of the mixer has a great impact on cell growth. The choice of mixer paddles not only requires efficient mixing characteristics, but also reduces the shear force on the cells. The main purpose of this improvement is to culture cells in a low-shear flow field environment. Currently, the most widely used type of agitator is propeller blades.
The propeller blades are mainly used to generate axial flow. They are mixed flow blades. They can generate circumferential and axial flow fields by themselves during stirring, which is conducive to the full dissolution and mixing of gas, liquid and materials, and the shear force of the flow field is small. . On the basis of the mixing paddle, different types of mixers have been developed by adding accessories and other improvements. Negative pressure is generated in the hollow shaft of the stirrer, so that the culture medium is sucked in from the bottom of the reactor and discharged from the top; a rotating filter is added and the cell-free culture medium is collected using the rotating filter.
bubble distributor
The structural form of the bubble distributor is closely related to the effect of dissolved oxygen in the culture medium. Bubble distributors commonly used in animal cell culture can be divided into L-shaped, ring-shaped, and microporous types. The L-type distributor has a simple structure and is easy to process. It is commonly used in reactors with small capacity. Due to the problem of uneven distribution of dissolved oxygen, it is not suitable for large-scale reactors. Annular bubble distributors are the most widely used, using 5 to 6 orifices with apertures between 0.5 mm and 1 mm.
Heating method
The culture temperature of animal cells is usually around 37°C, and the allowable control error range is ±0.25°C. The heat source mainly consists of biological reaction heat, stirring heat, radiation heat and ventilation heat. Heating methods include overall wall heating, bottom heating and side wall heating. Generally, jacketed water circulation, electromagnetic heat generation, and electric blankets are used to control the temperature in the reactor. No matter which method is used to control the temperature, the temperature adjustment must be gradually increased to avoid excessive temperature damage and cell apoptosis.
Non-stirred bioreactor
Non-stirred animal cell bioreactor
The biggest disadvantage of stirred bioreactors is cell damage caused by shear force. Non-stirred reactors produce smaller shear forces and have outstanding advantages in animal cell culture.
Its principle is to use a circulating air lift central air inlet, no stirring device, and a guide tube added to the traditional bubble tower. Its advantages are simple structure, convenient operation, relatively mild turbulence, little damage to cells due to shear force, and easy realization of high-density culture of animal cells. Since the enlarged airlift reactor cannot determine the operating range that is not affected by shear force, it is rarely used on a large scale.
Optimization measures
This section optimizes the height-to-diameter ratio and bottom radius of the reactor tank, the installation height of the agitator, baffles and other structures. Due to the different roles of each component in the flow field, the optimization target parameters of each component cannot be given. Only It can be optimized by a single factor based on the role of each component in the flow field with reference to the mechanical properties of CHO cells.
1. Height to diameter ratio optimization
The general selection range of bioreactor height-to-diameter ratio is relatively large, which is related to the specific reactor form. For airlift reactors, a slender structure is generally used, while for stirred bioreactors, the height-to-diameter ratio is generally selected to be 1, which is too large. This is because the mixing power of the stirred bioreactor comes from the stirrer. The mixing performance of a single stirrer generally does not allow the height-to-diameter ratio to be too large or too small, which is not conducive to the mixing of culture fluid. Based on domestic and foreign products and literature, this article determines the optimization range of the height-to-diameter ratio as 1 to 1.5.
The rotation speed adopts the usually selected 80r/min, and the baffle is fully integrated. Different tank bottom radii also have a significant impact on the statistical distribution of the velocity field of the reactor. R0=0.5t has no zero speed zone, fewer low speed zones, the best mass transfer efficiency and the least power loss.
Liquid streamline diagram on the longitudinal section at a certain instant in the quasi-steady state. Color indicates liquid velocity (m/s).
2. Tank bottom radius optimization
Using a flat bottom or other tank bottom with poor flow linearity is not conducive to the mixing of the flow field. No matter what optimization method is used, there will be a zero-speed zone, which is not conducive to the mixing of the bioreactor flow field. This article uses the hemispherical tank bottom as the basis to optimize the spherical tank bottom radius of the tank. Usually the semi-radius of the tank bottom is in a certain proportion to the tank diameter, and the range generally varies between 0.5 and 1. The flow field in the reactor not only has a near-zero velocity area (0-0.001m/s), but also has a higher volume percentage in the low-speed area (0-0.01m/s). Overall, the height-to-diameter ratio is 1/3 A better mixing flow field can be formed, which is beneficial to the transportation of nutrients, so the height-to-diameter ratio is 1/3.
Liquid streamline diagram on the liquid surface at a certain instant in the quasi-steady state. Color indicates liquid velocity (m/s)
3. Optimization of the number of baffles
In a bioreactor without baffles, no matter what type of agitator is used, the mainstream field will form a large vortex, dominated by laminar flow, which cannot form an overall circulation of the flow field and is not conducive to the exchange of nutrients. Cell growth and metabolism are inhibited. Generally, baffles are installed above 20L. The main function of the baffle is to convert circumferential flow into axial flow, so that the circumferential flow and axial flow of the main flow field can be balanced, and the fluid mixing in the reactor can be enhanced. After testing, compared with the three pairs of baffles, the other two solutions have an asymmetric velocity field distribution in the liquid surface area, which will form a large vortex turbulence in the mainstream field and produce a lot of foam, which is not conducive to the growth of cells. Moreover, the three pairs of baffles The speed distribution of the plate is also the most uniform, and in comparison, three pairs of baffles are the best.
Outlook
Animal cell bioreactors need to have a low-shear flow field environment, uniform liquid phase stirring, precise control systems, and easy linear scale-up culture. The amplification of the bioreactor culture process is a very complex technical problem. The biggest bottleneck in the design is the precise control of various parameters after amplification. This problem will be solved by comprehensive disciplines, involving fluid mechanics, computer science, bioengineering and other disciplines.
This article gives a detailed introduction to stirred, non-stirred and new bioreactors, and discusses issues such as their structural optimization. The purpose is to study the technological progress of bioreactors, understand the current situation and future development, and provide a basis for It provides some reference for selecting bioreactors that are more suitable for culture processes in the practical application of biological products R&D and production and for the research and development of bioreactors.