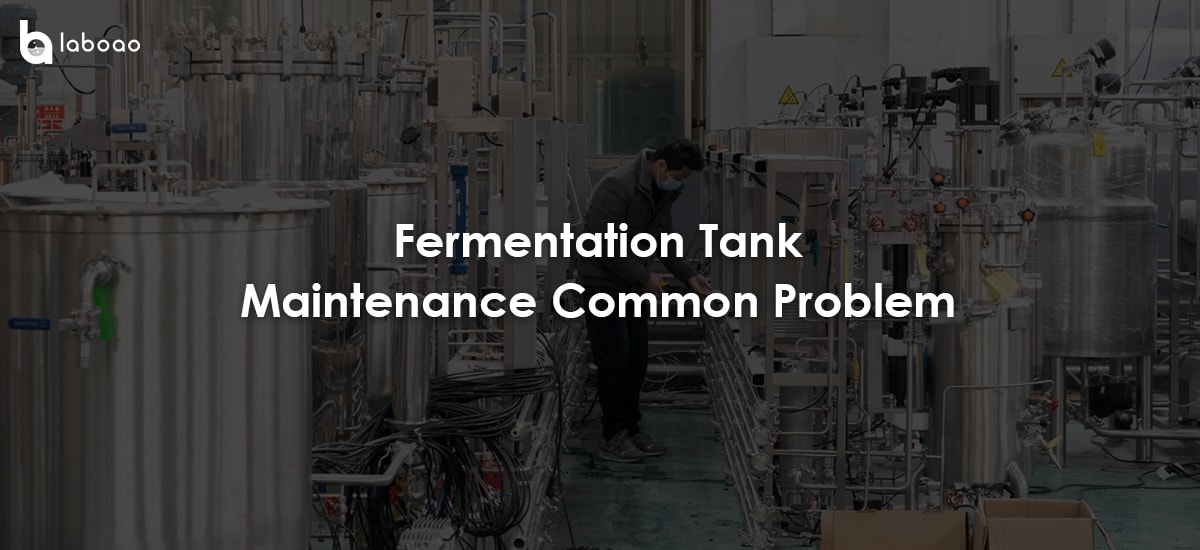
一. Inspection and maintenance of fermentation tank system
The maintenance and upkeep of the fermentation tank system can be divided into two methods: daily and regular. Both are indispensable.
1. Daily inspection and maintenance
(The monitoring content during equipment operation should be recorded accordingly)
Check whether the system pressure and tank pressure are stable within the specified range. Check whether the stirring system, temperature control system, and solenoid valve sound normal. Is the color of the culture medium normal? Whether the temperature and dissolved oxygen pH display parameters are consistent with the settings. Is the liquid level in the tank normal? Check whether the valve, pipe joints and interfaces are normal, and whether there is any leakage.
2. Regular inspection and maintenance
(1) Every three months, the equipment needs to be comprehensively inspected and corrected. Cut off all power, water, and gas (steam) sources.
(2) Carefully check whether all sealing rings and sealing ends of the system are in normal condition. If it is deformed, aged, scratched or damaged, it must be replaced. Check the integrity of the sterilizing filter. If it is damaged or clogged, replace it.
(3) Wear of motor carbon brushes and conditions of commutator, bearings, couplings, and stirring systems.
(4) Check all switches, buttons, electrical appliances, electronic components, fixing screws, and nuts of the electrical controller for looseness or heat.
二.Fermentation tank cleaning and maintenance
1. Cleaning
(1) The fermentation tank body is a place that is in direct contact with materials. The degree of surface finish and the cleanliness of internal components are factors that directly affect bacterial contamination. Therefore, the tank and related equipment must be cleaned promptly after each fermentation and before use again. When cleaning, attention should be paid to electrical components and electrode interfaces to prevent water from entering and moisture.
(2) Before cleaning, the PH and DO electrodes should be taken out and maintained according to their requirements.
(3) Cleaning the tank can be carried out with water and air inlet, motor stirring, and heating. If the water cannot be cleaned after repeated water changes, open the top cover and use a soft brush to scrub the internal parts of the tank. The method is as follows: control switch and power switch, remove the top cover electrode, motor and its connecting plug. Unplug the quick connector of the air inlet hose condenser and remove the upper hose and joint of the air inlet filter; remove the top cover vertically together with the stirrer, and place it horizontally on a flat table. Pad it well and do not collide with the shaft and impeller. Use a neutral Use detergent to scrub the tank and internal components.
(4) Note: When moving and cleaning the tank cover, you can only hold the sleeve or top cover, but not the mixing shaft, impeller and other easily deformable parts. While cleaning, some O-ring seals such as the tank and outlet valve should be inspected. If deformation, aging, scratches, etc. are found, they need to be replaced in time. After cleaning and reinstallation, the surface and tank racks should be wiped dry with a rag. Tighten the six fastening screws of the tank cover. The force should be balanced and the gap between the tank and the tank base should be balanced. Special care should be taken when cleaning glass fermentation tanks. Do not collide when disassembling and assembling. When tightening the fastening screws of the tank cover, the force must be balanced and the gap must be balanced to avoid damage to the glass tank.
2. Sealing test
(1) Install the electrodes, motors, cables, air inlet and outlet hoses, and condenser water inlet and outlet joints in place; after installation, conduct a tightness test on the ventilation (0.2MPa) in the tank.
(2) Tighten each interface, plug, and electrode fastening cap on the tank; open valves 207, 208, and 209 and the air compressor, adjust valve 206 to keep the tank pressure around 0.2MPa; unplug the quick connector on the DX , the tank pressure drop rate should be less than 0.02Mpa/h. Conduct a trial run of the system for 2-3 hours. If there are any problems, deal with them accordingly before it can be officially used.
3. Fermentation tank ready for use
(1) If culture and fermentation need to be carried out again in the short term, they should be sterilized. Then introduce sterile air and keep the pressure until use.
(2) If it is to be stopped for a long time, it should be sterilized, then drain the water tank and tank, loosen the fastening screws of the tank cover, take out the electrodes for maintenance and storage, drain the remaining water from the tank and each pipe, and close all Valve, power supply, cover with dust cover.
3. Precautions
(1) Before sterilization, the output pressure of the steam generator should be checked and adjusted to ensure that the pressure is ≤0.35Mpa (the value displayed on the steam generator pressure gauge). During the sterilization process, the air pressure in the tank should be checked to ensure that the pressure is <0.15Mpa.
(2) Before fermentation, the output pressure of the air compressor should be checked and adjusted to ensure that the pressure is ≤0.4Mpa (the value displayed on the air compressor pressure gauge), and the output pressure of the pressure reducing valve should be adjusted to ≤0.25Mpa. During the fermentation process, the air pressure in the tank should be checked to ensure that the pressure is ≤0.10Mpa. The use and maintenance of DO and pH electrodes must be carried out as required, otherwise they will be easily damaged. All electrical devices are strictly prohibited from water, moisture or contamination.